Print automation: Faster, easier, error-free
What was the issue?
It is not uncommon for orders to be placed at Delga Press where the corresponding artwork files are not print-ready. There could be several reasons for this, including but not limited to missing bleed, embellishments not set to overprint, and spot colours within CMYK, to mention a few. For the client, this inevitably results in a delay in returning a proof for them to review and approve, and ultimately this affects the delivery of the final order. Delga’s Systems & Pre-Press Manager explained:
Delga Press have recently invested in a new automation system which reduces the time it takes to process an order from what can sometimes be days, to minutes. To test this new system, Delga Press needed a willing client to work with; ideally, a client who could see the benefit of the automation. Delga approached long-standing client Mirage, one of the most experienced electronic cigarette retailers in the world, with a significant number of SKUs. Mirage saw the potential in such a project and were only too happy to jump on board to help, as Mirage’s Head of Design explains:
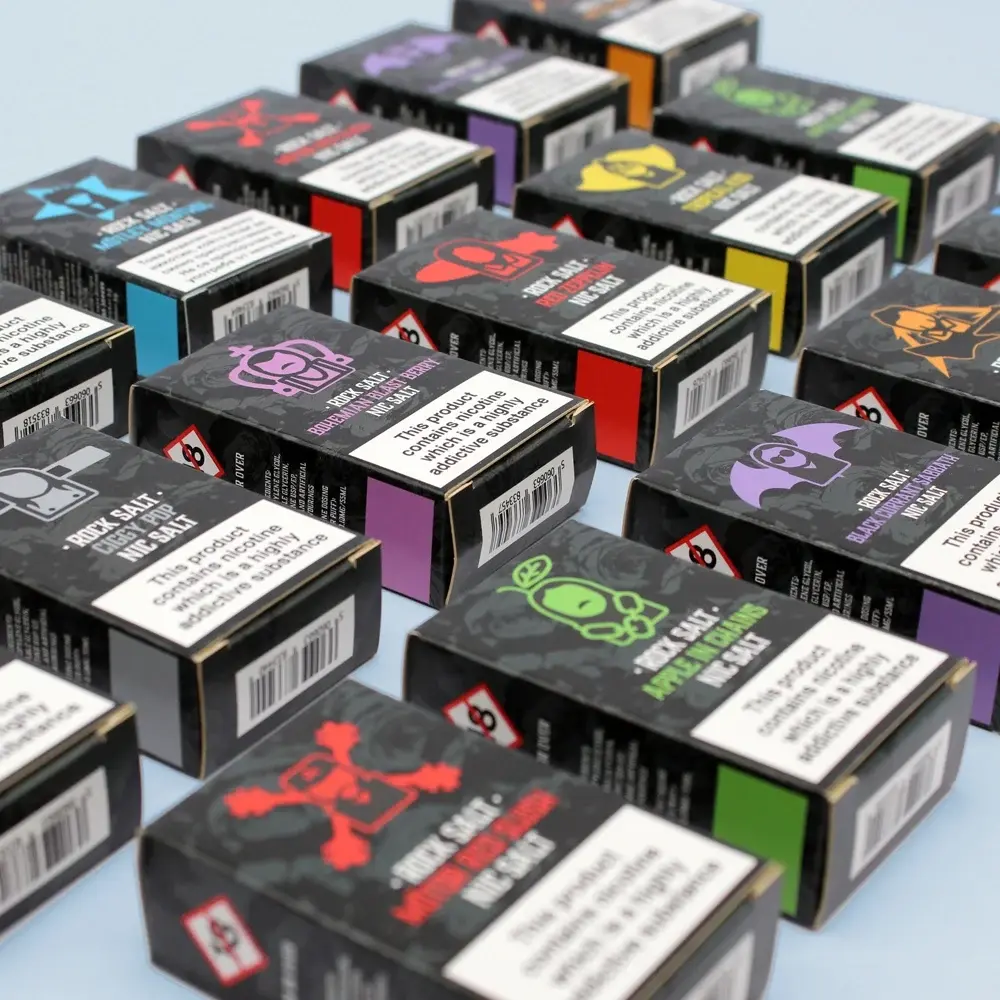
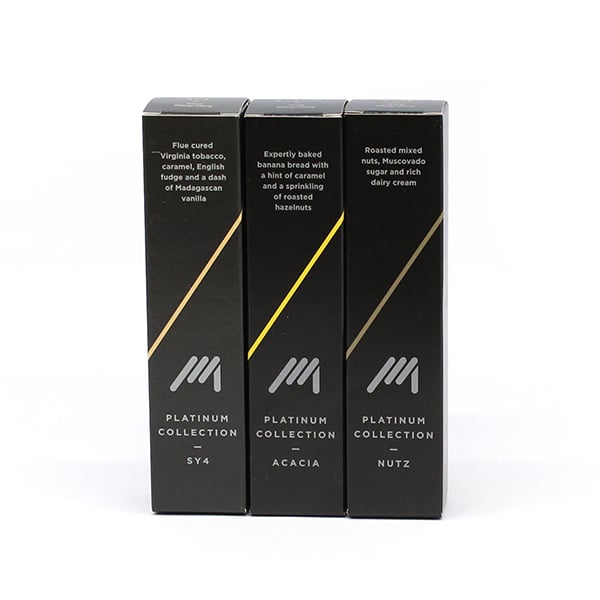
How did we solve it?
The new system required a process change on both sides. From the client’s perspective, Delga provided a prescriptive set of artwork specifications that each file must adhere to, and each file name should follow a specific convention. Providing this was all followed, files are submitted via Delga’s artwork submission portal, a proof is generated immediately and once approved via the portal, the file is automatically prepared for print and is scheduled accordingly throughout the factory. Once the client is used to the artwork specifications and the naming conventions required, this new process doesn’t cost the client any more of their time and saves Delga hours, even days of pre-press work and time. Ultimately, the client receives their proofs and final orders day’s sooner, Delga saves a significant amount of pre-press hours and there is zero room for error. To kick the process off, Mirage employees were invited to a video call to go over the requirements needed from their end. The meeting was chaired by Sales Office Manager Annika Inge and run by our experienced pre-press team. They were shown what would need to be implemented by their designers for the automation to run smoothly. This included a naming convention, decided by the client, that must be consistent with the PO and education on how to set up files for print and what checks to make before submitting the files to the portal.
The designers from Mirage were given free training and support on industry-standard formats for print-ready files, and they were also provided with a guide for future reference, and going forward our pre-press team are on hand to support them when needed. The feedback about the training was very positive:
What was the result?
An order from Mirage now takes minutes to process through the new automation system and less human intervention in the process from Delga Press means less room for error.
If files are provided in the correct format and with the correct naming convention then everything will sail through smoothly but, should there be any issues with the files, the system will alert our pre-press team so that the client can make the necessary adjustments and resubmit. The system is so smart that it will remove any incorrect artwork so when the new file is submitted there can be no mistaking which one is the correct and up-to-date version.
The automation process also has a proofing portal that allows the client to see an accurate display of what the file will look like printed. They are also able to toggle layers to check all elements are correct.
What this does is put the responsibility of the artwork into the hands of the client but not without plenty of training and support to ensure they know what they are doing, and as a result, doing it right becomes an autonomous process.
There are plenty of other benefits in addition to time-saving and error reduction. The automated process also can decipher the best layout for the artwork on the sheet so that waste is reduced, not only is this another cost-saving benefit but also an environmental benefit too.
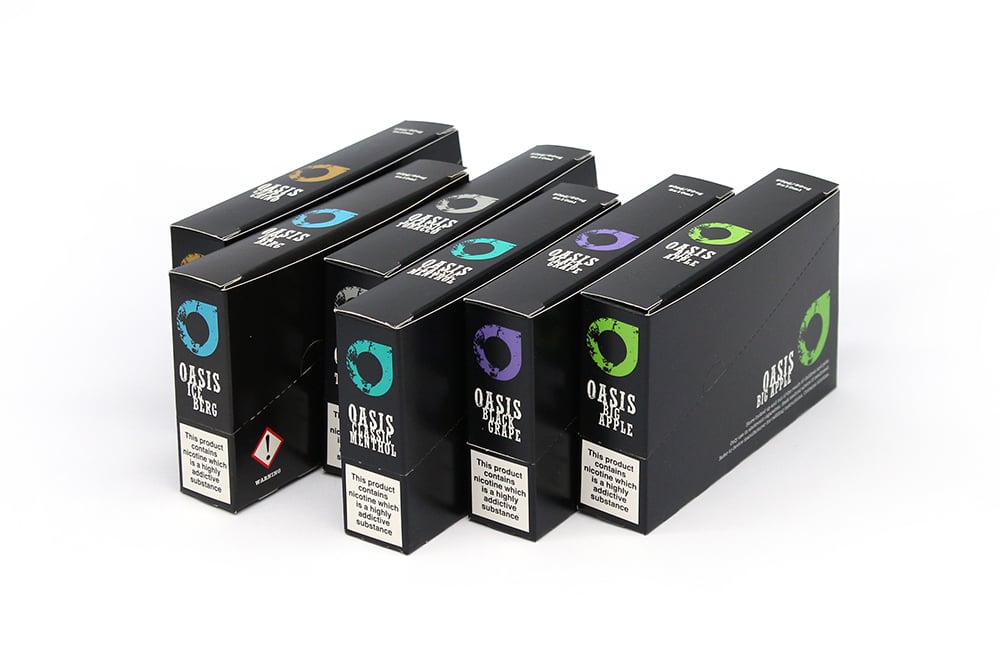
If you would like any more information about our packaging and automation services, please do not hesitate to contact us.